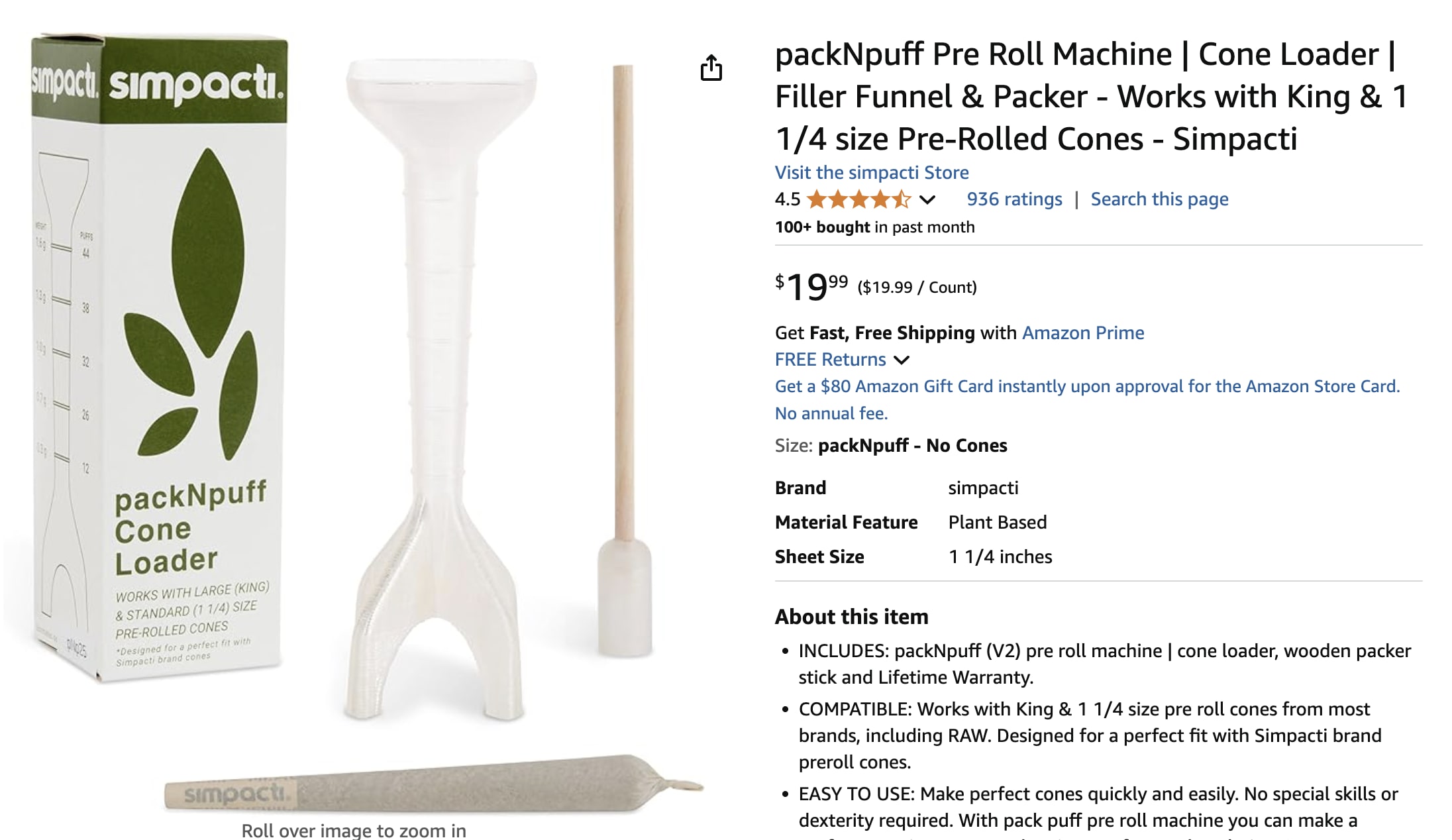
packNpuff: Sustainable Precision Cone Loader
Project Overview
packNpuff is a sustainable, 3D-printed cone loader designed to solve the challenge of efficiently packing pre-rolled cones to precise measurements. Born from direct industry experience, this innovative tool has revolutionized how consumers and businesses prepare pre-rolled cones with consistent results while minimizing waste of valuable plant material.
The Problem
While working in cannabis dispensary operations from 2011-2016, I identified a significant market gap: no efficient tools existed for preparing smaller pre-rolled cones. The industry standard was 1g joints, but our dispensary wanted to offer 0.25g options to meet changing consumer preferences. The manual process of preparing these smaller cones was inefficient, inconsistent, and created substantial product waste.
The Solution
packNpuff addresses these challenges by providing:
- Precision measurement with integrated guides allowing users to create perfectly sized portions
- Efficient loading through a specially designed funnel that fits pre-rolled cones perfectly
- Consistent packing with an included packing tool that ensures even distribution
- Versatile sizing accommodating both 1¼ and king size cones (in v2)
- Sustainable manufacturing using plant-based PLA plastic with zero single-use plastics
I also pioneered the "speed pack method" that allows users to load all material at once and quickly achieve an evenly packed cone, significantly reducing preparation time.
Technical Implementation
Sustainable Manufacturing
packNpuff is produced using Fused Filament Fabrication (FFF) 3D printing technology with plant-based PLA plastic. This approach allows for:
- On-demand production to minimize waste
- Zero single-use plastics in both product and packaging
- Recyclable and biodegradable materials
- Packaging made from recycled materials
Product Evolution
Version 1 (2016-2019):
- Required dual extrusion printing with high maintenance needs
- Compatible only with 1¼ size pre-rolled cones
- Initial market validation model
Version 2 (2019-Present):
- Redesigned for single extruder printing, significantly improving production efficiency
- Enhanced compatibility for both 1¼ and king size cones
- Improved ergonomics and user experience
- Exposes the bottom of the cone during filling to prevent user error
- Designed with future injection molding transition in mind
- More aesthetically pleasing design
Challenges and Solutions
Technical Production Challenges
Challenge: Determining optimal 3D printing parameters that balanced quality with production efficiency.
Solution: Extensive testing to identify the ideal layer heights and print settings that deliver consistent quality without excessive production times.
Technical Support Limitations
Challenge: Running a 3D printing operation when comprehensive resources weren't widely available online.
Solution: Developed expertise in printer maintenance and troubleshooting through hands-on experience, becoming self-sufficient in manufacturing operations.
Business Model Pivot
Challenge: Initial B2B sales strategy to dispensaries was less successful than anticipated.
Solution: Pivoted to direct-to-consumer sales through Amazon, which dramatically increased reach and sales volume.
Outcomes and Impact
packNpuff has achieved remarkable market validation:
- Customer satisfaction: 4.6-star rating with over 930 reviews on Amazon
- Market leadership: Recognized by customers as the best product in its category
- Sustained success: Consistently strong sales from 2017 to present, despite increased competition
- Environmental impact: Eliminated single-use plastics from the production process
- Family business growth: Expanded to include family members in production, packaging, and fulfillment since 2023
Future Development
The roadmap for packNpuff includes:
- Manufacturing evolution to injection molding when demand volume justifies the transition
- Version 3 design incorporating additional user feedback from V2 customers
- Continued focus on sustainable materials and environmentally responsible manufacturing
- Expanding product line based on successful core technology
Technologies Used
- Manufacturing: FFF 3D Printing
- Materials: Plant-based PLA plastic
- Packaging: Recycled materials, zero single-use plastic
- IP Protection: Patent secured for the design
This project demonstrates how identifying a specific industry need and addressing it with sustainable manufacturing methods can create a successful product with long-term market appeal. packNpuff transformed from a solution for a single dispensary's operations challenge into a thriving direct-to-consumer product with strong customer loyalty.